Casting Process
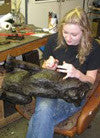
THE CRAFT OF VANISHING MOLD
Lost wax casting, an ancient technique spanning millennia, remains shrouded in mystery for most, its intricacies often eluding comprehension.
Even as mechanization has streamlined the bronze casting method employing the lost wax technique, the fundamental procedure echoes the very one pioneered by the Chinese during the 2nd millennium BC.
THE RUBBER MOLD
Initially, the artist crafts an original sculpture using a diverse range of materials such as stone, wax, clay, wood, or pottery.
Subsequently, this creation is enveloped in silicone rubber molding substance, generating two halves of rubber molds (each comprising a front and a back segment). To ensure structural integrity and steadfastness across subsequent applications, a fiberglass outer casing is affixed to the rear of each mold.
These molds stand as the sole elements to endure in the casting sequence, with all other components being fashioned anew for each casting endeavor.
While automation has modernized the lost wax technique in bronze casting, the fundamental procedure remains akin to the one pioneered by the ancient Chinese during the 2nd millennium BC.
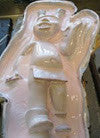

THE WAX POSITIVE
Once the molds are done, the insides are coated with layers of wax. The halves are then bound together and wax poured inside to complete the wax image being created.
Once the wax has cooled, the mold is peeled away, yielding a wax image (the wax positive") duplicating the original sculpture.
This image must then be "touched -up" to remove any seam lines, scratches or other flaws, as well as to recreate any pattern or texturing that was lost or damaged when the wax was made.
The quality of the finished bronze relies on a clean, high quality mold and an impeccably recreated wax image that is as near to perfect as possible.
GATING
Following this, the subsequent phase known as "gating" involves affixing a succession of tubes and channels. These conduits serve the purpose of enabling the molten bronze to course its way downward within the ceramic shell, while concurrently permitting the expulsion of heated gases.
These channels, often referred to as sprues, come into existence by attaching wax rods to the finalized wax configuration, positioning them strategically at spaced intervals.
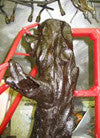
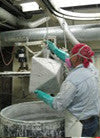
CERAMIC SHELL CASTING
Once the gating process reaches its conclusion, every wax mold undergoes immersion in a solution comprising liquid ceramic silica-sand amalgam. This immersion ensures a comprehensive enveloping of the form both internally and externally. Within the wax, designated apertures known as "patches" have been introduced, affording access to the interior of the form.
Continuing from this point, the form is then subjected to a sequence of 6 to 12, or potentially more, consecutive immersions across several days. This extended procedure results in the gradual accumulation of layers upon the form's surface until the sought-after thickness of the ceramic shell is accomplished.
LOST WAX
After the ceramic shells have undergone complete drying, they are introduced into an autoclave. In this apparatus, the wax within is subjected to melting, thus affirming the aptness of the term "lost wax." This melted wax is subsequently reclaimed and can be employed anew.
Subsequent to this process, the shells proceed to be solidified within a kiln. This curing procedure imparts resilience to the shells, rendering them capable of enduring the intense temperatures accompanying the pouring of molten bronze into their confines.
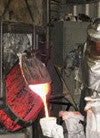
THE POUR
Bronze ingots are subjected to melting at a temperature around 2000°F, after which they are carefully poured into the ceramic shells that have undergone the curing process.
As the sculpture gradually cools, the ceramic shell initiates a detachment from the bronze surface, resulting in a distinctive popping effect.
In the subsequent stages, this ceramic shell is meticulously shattered, employing tools like hammers and chisels. This action facilitates the removal of excess metal materials, revealing the final form of the sculpture.
SANDBLASTING
Subsequently, the cast piece undergoes sandblasting as a preliminary step for the forthcoming metal finishing process.
If any components of the sculpture were cast individually, they are then meticulously reattached through welding. Concurrently, any evident seam lines or imperfections are meticulously eliminated or, as the term goes, "chased".
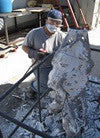

TEXTURING
Ultimately, any lost or impaired texturing, arising from the casting or welding phases, is meticulously revitalized.
Following this, the sculpture enters the polishing phase, meticulously prepared for the forthcoming application of the patina.
PATINAS
The array of diverse hues and finishes attainable on cast bronze sculptures are referred to as patinas.
These diverse shades, designs, and textures, achieved through a harmonious interplay of chemicals and heat, are enhanced by meticulous stippling or airbrush spraying techniques. The final result is preserved through the application of lacquer and waxes to ensure longevity and visual allure.
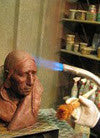
LIMITED EDITIONS
The majority of bronze artworks belong to a "limited edition," encompassing a predetermined quantity of castings.
The determination of this edition number typically takes place post the initial casting of the piece and is personally chosen by the artist. Each sculpture is then imprinted with an individualized edition number (e.g., 1/100), marking the culmination of the bronze sculpture production process.